The integration of additive manufacturing technologies into the production process of orthopedic insoles has ushered in an era of unprecedented customization, shaping the insoles according to the specific anatomical forms of each patient. The synergy between continuously evolving materials and advanced 3D printing technologies has not only refined production precision but has also eliminated manual processes, significantly reducing time, costs, and the use of raw materials.
Accommodative or diabetic insoles are orthopedic devices designed to provide specific support to the feet of individuals with diabetes or foot issues. These insoles ensure additional comfort, cushioning, and protection for sensitive feet, often compromised by diabetes-related complications such as peripheral neuropathy or reduced blood circulation.
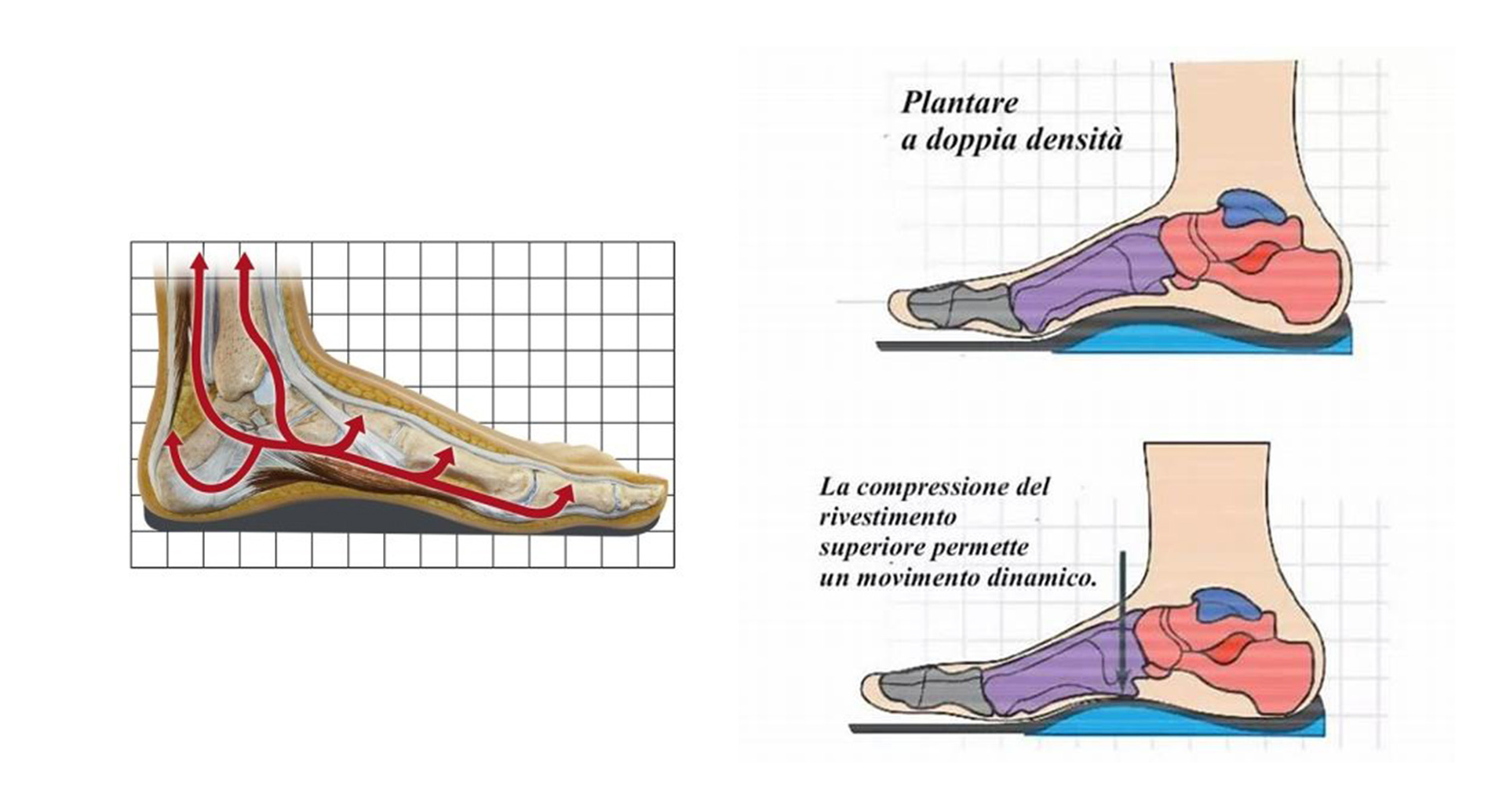
Designed to increase the foot's contact surfaces in order to reduce pressure peaks, they ensure a better distribution of the load. Commonly used in casual footwear, sports shoes, specialized slippers, or work and safety shoes, accommodative or diabetic insoles exhibit fundamental characteristics:
- Cushioning: crafted with shock-absorbing materials to reduce pressure on the feet during walking;
- Arch Support: provides support to the arch of the foot and improves weight distribution, reducing pressure on critical points of the foot;
- Soft Material: often made with soft and flexible materials to prevent friction or pressure points, reducing the risk of injuries or ulcers;
- Customization: adaptable to the specific needs of the patient, such as foot deformities or prosthetics;
- Protection: guards against friction, calluses, ulcers, and skin injuries, reducing the risk of complications in diabetic patients.
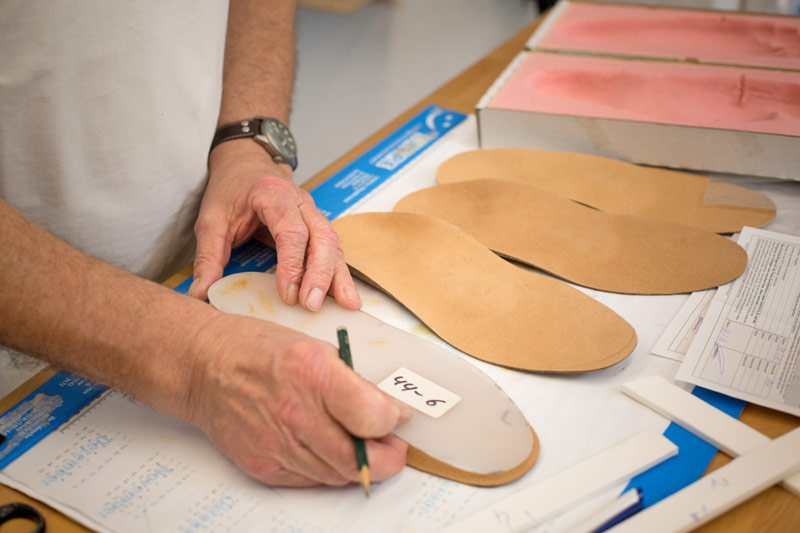
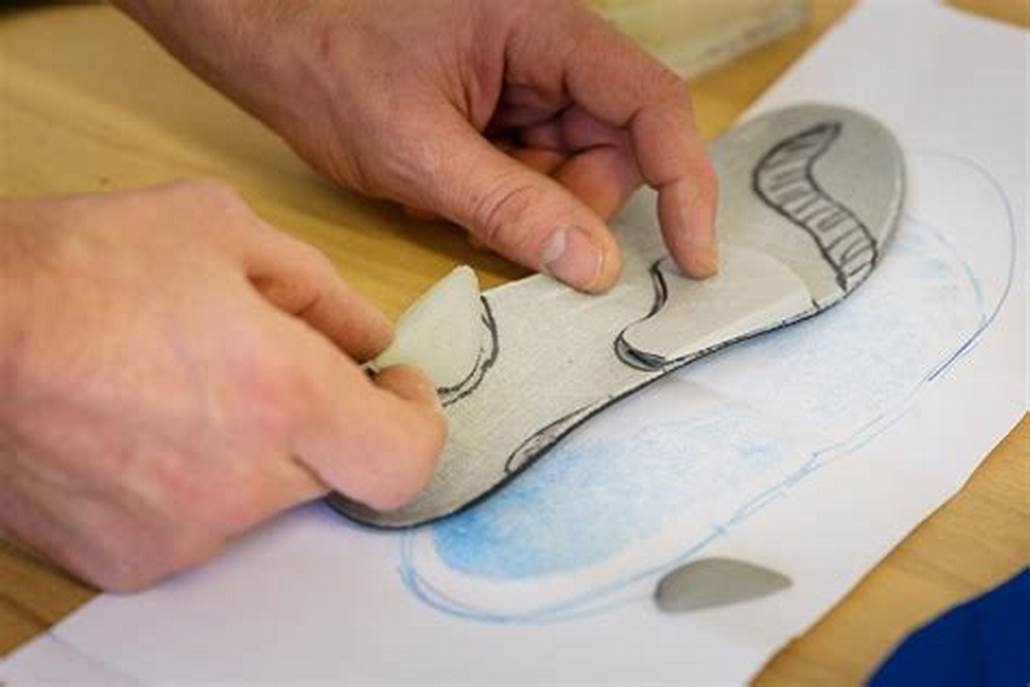
Traditional insoles, manually crafted with foams of varying hardness, generate up to 90% waste. The use of additive manufacturing technologies, particularly the fused filament fabrication (FFF) technology, revolutionizes this process, enabling the production of complete insoles with various cushioning zones tailored for patient comfort. This approach is not only economically advantageous due to minimal labor requirements but also occurs in a decentralized manner, directly at the professional's workshop.
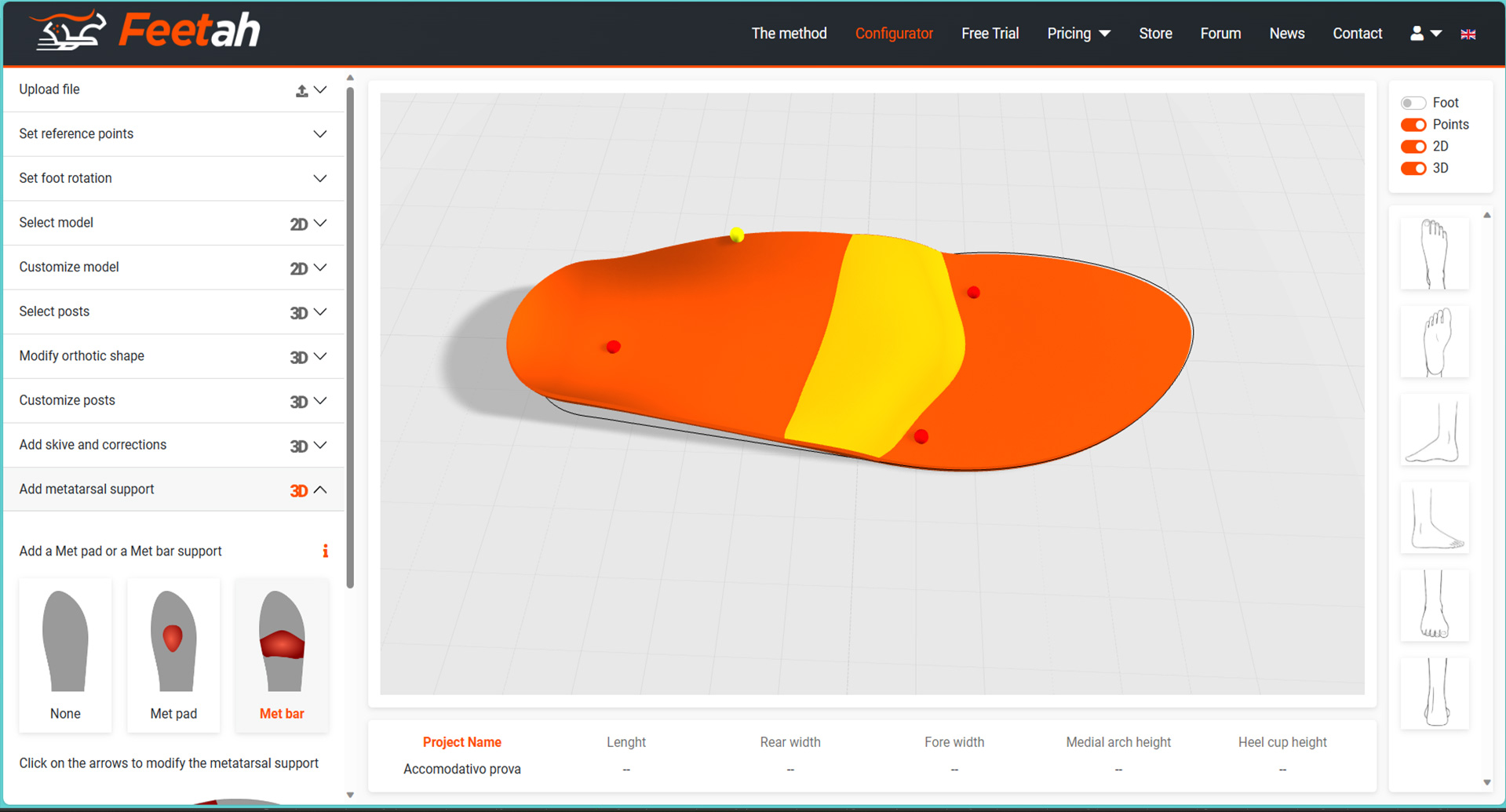
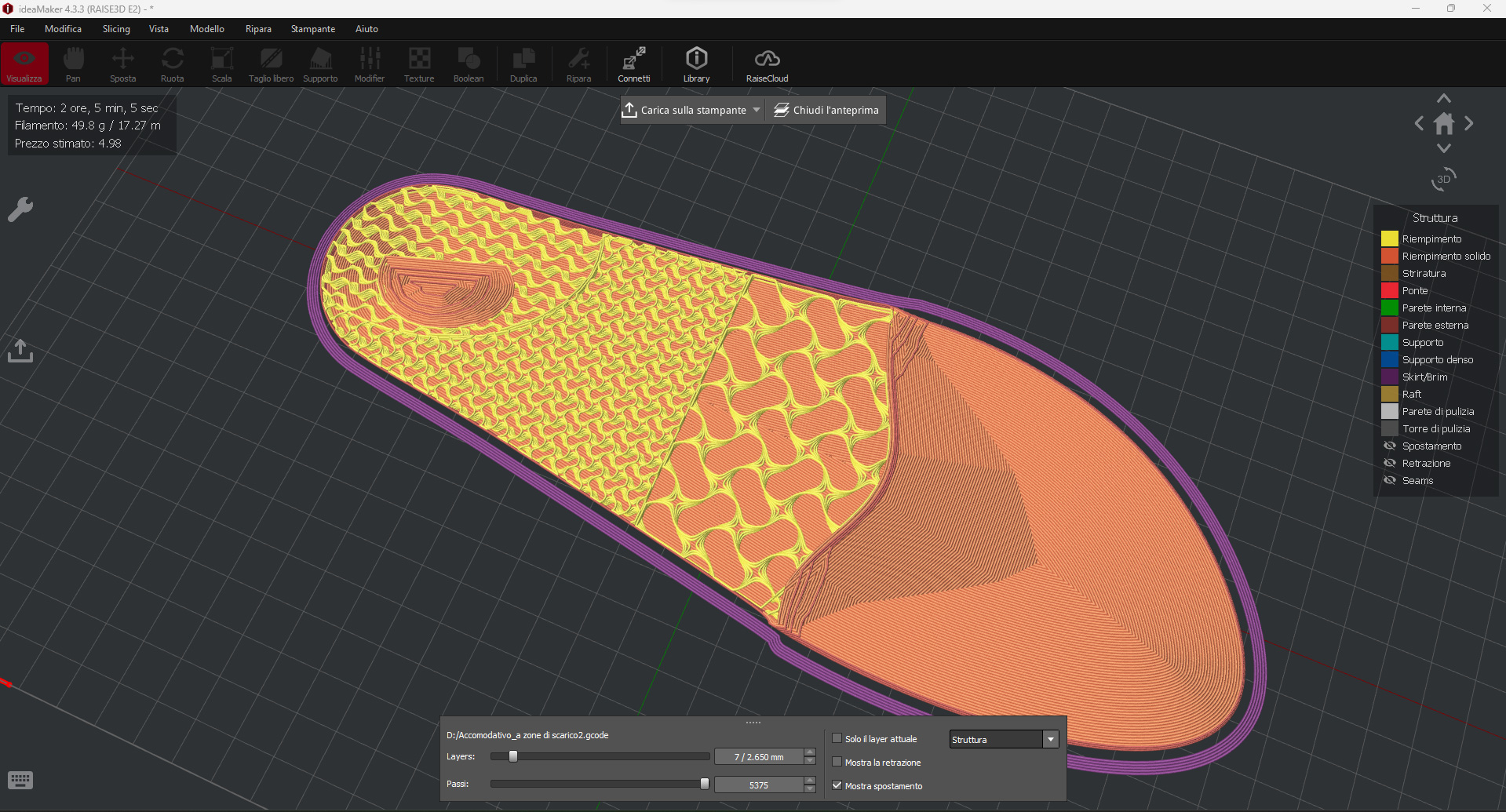
The continuous evolution of materials and technology used in 3D printing processes has driven the CreaMED team to seek the optimal combination of elastomeric materials and printing parameters. The thermoplastic polyurethane (TPU) with a Shore hardness of 85A from the BASF brand has proven to be one of the most high-performing elastomeric polymers on the market, offering both strength and softness to the insole with the right formulation of filling between geometry and density. This results in achieving an optimized cushioning structure in terms of ergonomics and lightweight, weighing only 30 grams and processed efficiently in just 2 hours using a 0.6mm diameter nozzle and a 0.4mm layer height. This approach allows for the customized production of a complete pair of insoles in just 4 hours.
The workflow that uses 3D technologies thus allows the professional podiatrist to definitively break free from traditional manufacturing processes, delegating the entire production phase to the machine and freeing up time for patient care. This results in saving up to 70% of the time typically spent on manual fabrication.
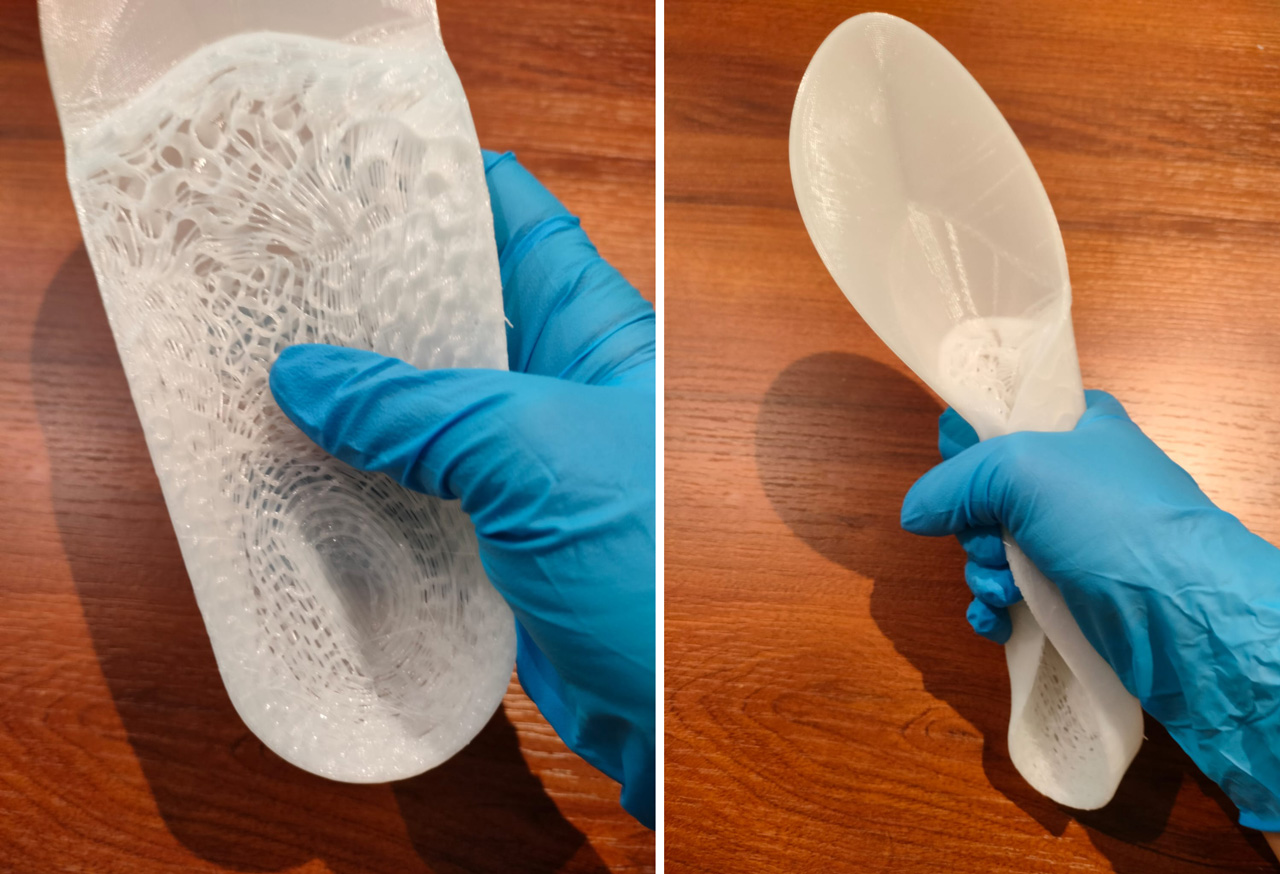
This is made possible using the Raise3D E2 desktop 3D printer, a compact, practical, and user-friendly solution. Equipped with IDEX technology, which optimizes the simultaneous printing of a pair of insoles, this printer is perfectly suited for the industry, designed to work with a wide range of materials, both standard and technical. In this way, it can meet all plantar therapeutic needs, ranging from corrective solutions to those specifically accommodative for diabetic therapy.
The complete digital evolution of the orthopedic professional's studio has never been closer.